Morse taper, clamping with conventional drilling, that's how it is!
In the field of drilling, we still sometimes get questions regarding the holder. Which holder do I need? My holder runs conical with an internal piece of thread at the end, which one is that? I have an old machine, is it still the same? With such a ''tab'' you can milling, can't you? We would like to give you some explanations to get you started with recordings for conventional drilling and milling!
Tool clamping with a conventional drill
For conventional drilling machines, we use the Morse taper feed. This guarantees reliable clamping and also enables rapid tool changes possible. The Morse Taper is also often described using the abbreviations MK (Morse Taper), MC (Morse Taper) or MT (Morse Taper). A Morse Taper is used to clamp machining tools (such as spiral drills, drill chucks and reamers) in, for example, (industrial) table and column drilling machines and lathes. The size of the taper shank corresponds to the matching toolholder.
A Morse Taper can be recognised by a slightly conical take-up shaft. The Morse Taper is a standardised tool holder according to DIN 228
The Morse Taper comes in two forms, type A and type B.
Type A is recognisable by a piece of internal thread at the end of the cone; this is used exclusively with rotary drills or milling machines with a threaded rod threaded rod
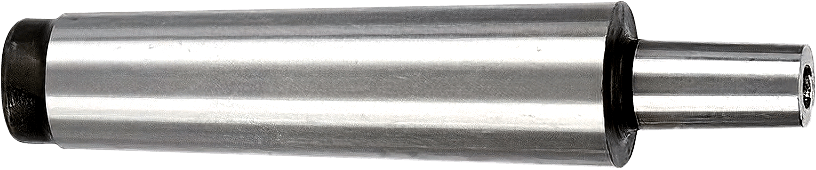
Type B is identified by a 'tab' (extruder lip) at the end. This allows you to easily 'tap' the tool out of the machine using a drive key from the machine with the aid of an extruder spear. This allows you to quickly change tools. Type B is the most common holder for conventional drilling and is used in table and column drills

Morse Taper Holders available in 7 different sizes
Of these, Morse Conus with size 2,3 & 4 are by far the most commonly used sizes for drilling. Here is an overview of the sizes.
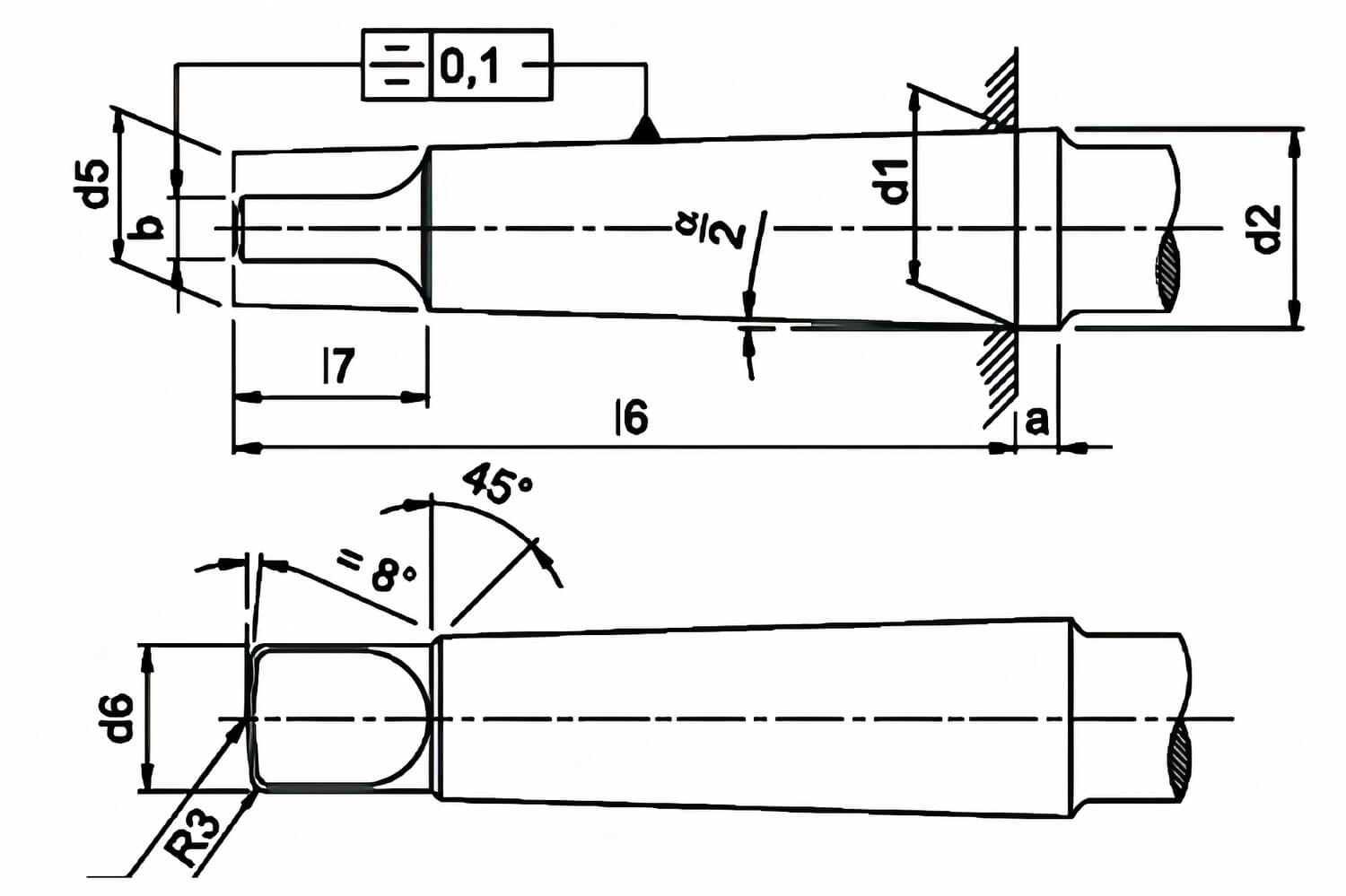